Burnishing
Finishing for steels
Hot burnishing is a surface finishing technique that gives steels a uniform coloring and increased corrosion resistance. Through controlled chemical reactions, an oxide layer is obtained that protects the metal and enhances its appearance, making it suitable for a variety of industrial applications.
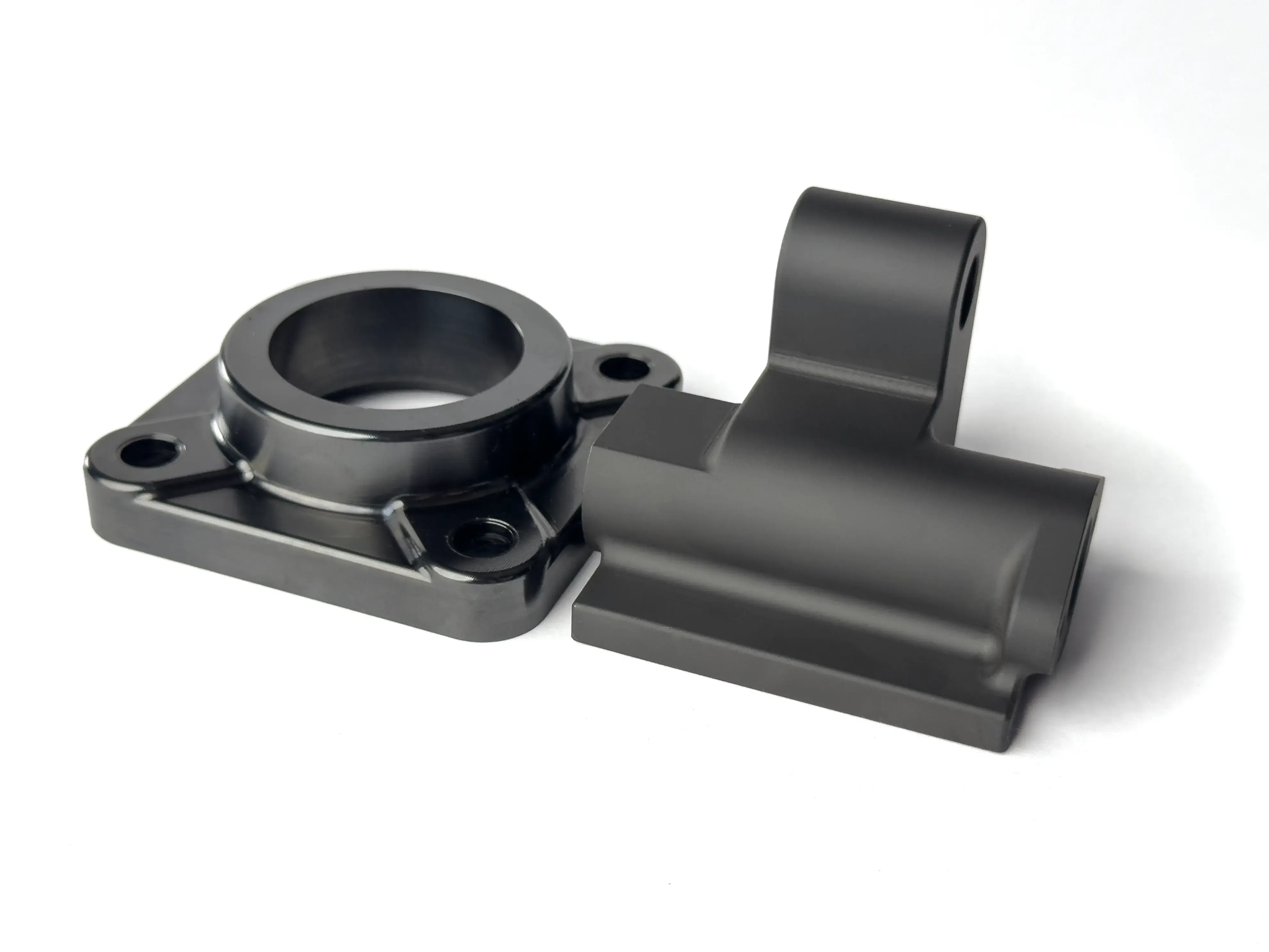
PROS
- Aesthetic improvement
- Corrosion protection
- No dimensional alteration
- Improved wear resistance
CONS
- Limited protection
- Need for maintenance
- Limited compatibility
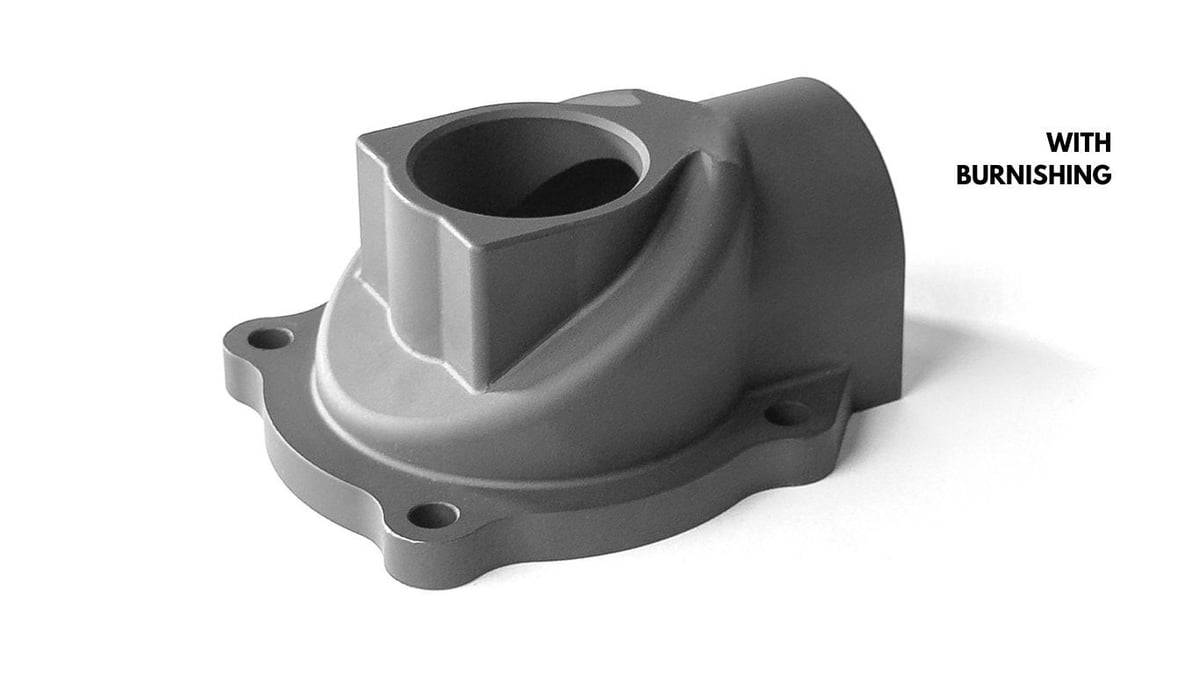
ADVANTAGES OF BURNISHING
Protection from corrosion
One of the main advantages of heat burnishing is the protection it offers against corrosion. The ferrous-ferric oxide layer formed during the process creates a surface barrier that slows the action of weathering and limits the formation of rust. However, for this protection to be effective over time, a layer of sealing oil or wax must be applied, which reduces the possibility of moisture penetrating the metal surface. This treatment is especially useful for components exposed to moderately aggressive environmental conditions, such as mechanical tools and firearm parts.
No dimensional changes
Another key aspect of heat burnishing is that it does not cause significant changes in the dimensions of treated components. Unlike other finishing processes, such as chrome plating or galvanizing, which add a layer of material to the metal surface, burnishing is a chemical treatment that acts on the surface itself without changing dimensional tolerances. This feature makes it ideal for precision parts, such as gears and measuring tools, where even small dimensional variations could compromise the functionality of the part.
Improved wear resistance
In addition to corrosion protection, heat burnishing helps improve the wear resistance of treated components. The oxide layer formed on the metal surface reduces friction between moving parts, improving smoothness and decreasing the risk of seizing. This effect is particularly appreciated in gears, pins and cutting tools, where less wear results in longer operating life and reduced maintenance costs. In environments where contact between metal surfaces is frequent, burnishing is an excellent solution for extending the service life of components.
INSTANT QUOTE FOR YOUR BURNISHED PARTS
free instant quoteMatte burnishing
COMMENT
Hot burnishing of steels is a surface treatment aimed at improving the appearance, corrosion resistance, and in some cases the tribological characteristics of metal components. This process is often used in the mechanical, weapons, and other industries where it is critical to protect metal surfaces from oxidizing and environmental agents.
Principles of burnishing
Burnishing is a chemical process that results in the formation of a layer of iron oxide on the surface of steel. This layer, generally black or bluish in color, not only enhances the aesthetics of the part but also offers some protection against corrosion. However, unlike other protective treatments such as galvanizing or chrome plating, burnishing does not form an additional coating, but chemically transforms the surface of the metal itself.
The heat burnishing process
There are several variations of the burnishing process, which can be divided into cold burnishing, hot burnishing and steam burnishing. Cold burnishing is performed by the use of chemical solutions at room temperature or slightly above. It offers less protection than hot burnishing and is mainly used for aesthetic reasons. Hot burnishing involves immersing the parts in hot salt solutions, generating a protective layer of black iron oxides. Steam burnishing is mainly used in the tool and gear industry to improve wear resistance and reduce friction. Of these, hot burnishing is the most widely used and valued for its excellent protective properties.
Hot burnishing is carried out through a series of well-defined steps that must be performed with precision to achieve optimal results. The standard process includes surface preparation, immersion in the burnishing solution, rinsing and neutralization, and finally oiling or sealing. Surface preparation is essential to remove any traces of grease, oils, oxides or impurities. This step may include degreasing with solvents or alkaline detergents, pickling with acids such as hydrochloric acid or sulfuric acid to remove oxides and rust, and washing with demineralized water to avoid contamination during subsequent treatment.
After preparation, the parts are immersed in a burnishing solution, typically composed of alkali salts such as sodium or potassium nitrates and nitrites, maintained at temperatures between 130 and 150°C. During this phase, the chemical reaction occurs that leads to the formation of the surface layer of ferrous-ferric oxide (Fe3O4), known as magnetite. After immersion in the burnishing solution, the parts are thoroughly rinsed with water to remove chemical residues. This step is crucial to avoid contamination and improve adhesion of the protective layer. To further improve corrosion protection, the burnished parts are dipped in protective oils or sealing waxes. This step serves to create an additional barrier against moisture and weathering, increasing the durability of the finish.
Advantages of heat burnishing:
Hot burnishing offers several advantages over other surface treatments, including:
-
Aesthetic enhancement: the black or blue coloring gives a professional and attractive appearance to metal parts.
-
Corrosion protection: although it does not offer absolute protection, the final oiling process helps prevent oxidation.
-
No dimensional alteration: unlike other coatings, burnishing does not add significant thickness to the metal surface, making it ideal for parts with tight tolerances.
-
Improved wear resistance: in some applications, the thin oxide layer reduces friction and improves the wear resistance of components.
Disadvantages and limitations.
Hot burnishing offers several advantages over other surface treatments, including:
-
Limited protection: the oxide layer is not particularly thick and, without proper oiling, may not offer sufficient protection in very aggressive environments.
-
Need for maintenance: burnished parts must be periodically treated with protective oils to maintain their corrosion resistance.
-
Limited compatibility: burnishing works best on carbon steels and some alloys, while it is not effective on stainless steels and other materials.
Applications
Because of its advantages, hot burnishing is used in a variety of industries. In the arms industry, it is used for finishing gun barrels, pistols and other firearms, providing corrosion protection without altering the mechanical properties of the metal. In the mechanical industry, it finds use on gears, screws, bolts and tools to increase their operational life. In the automotive industry it is used for precision components and engine parts subject to adverse environmental conditions. Finally, in the measuring instrument industry, it improves the reliability and durability of calipers, micrometers and other precision instruments.
Conclusion
Hot burnishing is a surface treatment widely used to improve the aesthetics, corrosion resistance, and durability of steel components. Although it has some limitations, its advantages make it an excellent choice in many industrial applications. For best results, it is essential to carefully follow all steps in the process and ensure that treated parts are properly maintained over time.
Questions and answers
Burnishing is a chemical surface treatment applied to metals, particularly steels, to improve their appearance and corrosion resistance. The process involves the formation of a layer of iron oxides that gives the material a dark color, typically black or bluish, without significantly altering its dimensions or mechanical properties.
The main difference between hot burnishing and cold burnishing concerns the process and effectiveness of the treatment. Hot burnishing is done by immersing the metal in heated salt solutions between 130 and 150°C, generating a uniform layer of iron oxides with increased corrosion resistance. Cold burnishing, on the other hand, uses chemical solutions at room temperature or slightly above, producing a similar aesthetic finish but with less protection against corrosion.
Weerg uses hot burnishing because it provides greater durability and quality of surface finish.
Burnishing primarily serves to protect metals from corrosion, improving their appearance with a uniform dark color. It also helps reduce friction between contacting surfaces, improving wear resistance. In industries such as mechanical engineering, automotive and weapons, it is widely used to prolong the service life of metal components.
Burnishing chemically modifies the surface layer of the metal by transforming it into iron oxides (Fe3O4), creating a protective barrier against rust and moisture. This treatment does not significantly alter the size of the part and, when combined with protective oils, further increases weathering resistance.
3-SECOND NO-OBLIGATION QUOTE
DO YOU WANT TO TURN YOUR CNC PROJECT INTO REALITY?
Upload your 3D file to take your parts production a step further.
free instant quote