Nylon PA12
Versatile, suitable for the rapid and precise production of parts
Nylon PA12, used in MJF technology, is an ideal technical material for the rapid production of prototypes and functional parts. It allows productions from 1 to 10,000 parts with excellent quality and design freedom. It represents a real alternative to injection moulding, with advantages in terms of flexibility and customisation.
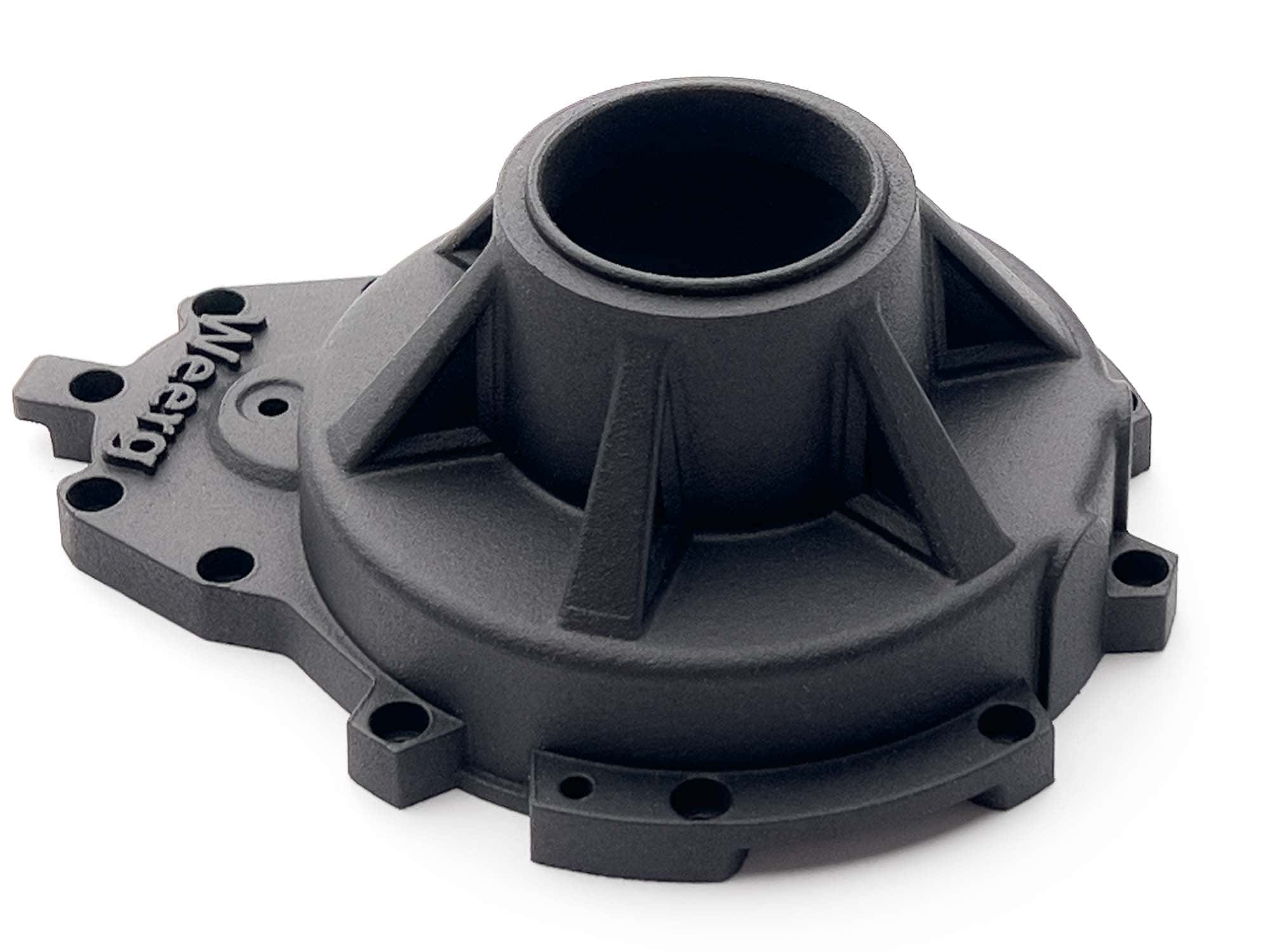
PROS
- From 1 to 10.000 pieces in 3 days
- Good chemical resistance
- Real injection molding competitor
- Parts are 100% solid and constructed without supports
- UL-certified
CONS
- Limitations related to high thicknesses or too massive parts
- Parts with wide flat surfaces can warp
MAIN FEATURES
- 3D printing process: MJF
- Tolerances: ±0,30mm < 100mm ; ±0,3% > 100mm
- Max size: 380 x 284 x 380 mm ; 15 x 11.2 x 15 in
- Lead time: <2 days
- Available finishes: dyeing, vapor smoothing, semi-matt, semi-gloss and metallic painting
NYLON PA12 3D PRINTING VIDEO GALLERY
Highly functional
Highly functional parts with excellent mechanical properties. Nylon PA12 is characterised by extraordinary tensile, abrasion and impact resistance. This makes it ideal for the production of final functional parts that retain the same characteristics as injection-moulded PA12. Due to its superior mechanical properties and durability, PA12 is an excellent choice for industrial and technical applications.
Excellent mechanical properties
Nylon PA12 offers remarkable temperature resistance, making it suitable for both high and low temperature environments. It has a high surface finish and excellent dimensional stability, ensuring extremely accurate prints thanks to HP's Multi Jet Fusion (MJF) technology. Its mechanical properties make it perfect for applications requiring reliable and durable materials.
Very easy to paint
Weerg offers a wide range of RAL colours for 3D printed parts made in Nylon PA12, allowing production in a variety of different colours and finishes. However, Nylon PA12 is very easy to paint with normal acrylic spray paint, giving you the freedom to customize your parts with the colours you prefer. This makes it perfect for creating detailed patterns and parts with unique colours, giving your prints the perfect finish!
QUOTE NOW YOUR NYLON PARTS
free instant quoteNYLON PA12 IMAGE GALLERY
COMMENT
Nylon PA12 is one of the most versatile and widely appreciated materials in the world of industrial 3D printing. Thanks to its unique combination of mechanical properties and excellent technical performance, PA12 is suited for a wide range of applications that demand strength, flexibility, and precision. Perfect for both prototype production and final functional components, nylon PA12 is ideal for projects where reliability and durability are critical.
What is Nylon 12?
Nylon PA12, also known as polyamide 12, is a high-quality engineering plastic belonging to the polyamide family. Thanks to its chemical structure, PA12 offers excellent chemical resistance and exceptional dimensional stability, even under thermal and mechanical stress. These characteristics make it highly valued across industries such as automotive, aerospace, electronics, and industrial component manufacturing.
Production in PA12 with HP Multi Jet Fusion Technology
We manufacture your creations in PA12 using the HP Multi Jet Fusion (MJF) 3D printing technology, one of the most advanced techniques in additive manufacturing. With this technology, the parts are 100% solid, ensuring maximum strength and durability without the need for support structures during the printing process. This gives designers unparalleled design freedom, allowing the creation of complex geometries, intricate intersections, and finely detailed parts that would be challenging or impossible to achieve with traditional manufacturing methods. The combination of PA12's versatility and MJF’s capabilities results in high-quality, functional parts produced quickly, without compromising precision or strength.
Pro
Fast Production: Thanks to MJF technology, nylon PA12 allows the production of 1 to 10,000 pieces in just three days, making it ideal for the fast production of prototypes and finished products.
Strength and Durability: The combination of extraordinary strength and flexibility makes this material perfect for a wide range of industrial applications.
Excellent Chemical Resistance: Resistant to many oils, greases, hydrocarbons and solvents, nylon PA12 proves perfect for applications in areas such as the chemical industry, automotive or medical equipment manufacturing.
Dimensional Stability: Parts moulded retain their original shape and size even under stress or extreme environmental conditions, ensuring dimensional accuracy and consistency essential in many industries.
Cons
Thickness limitations: While nylon PA12 is ideal for many 3D printing projects, it has limitations when it comes to thicker parts or very massive components. This may require more careful design or the use of specialised printing techniques.
Parts with large flat surfaces can deform: During the 3D printing process, the material is heated and if different parts of the part cool at different speeds, this can generate internal tensions in the material. These tensions can cause parts of the part that cool faster to bend or warp, creating deformations especially with large flat surfaces. In order to avoid warping, post-production work or design adaptation may be required to ensure dimensional stability.
Applications of Nylon 12
Aerospace: Nylon PA12 is widely used in the aerospace industry for the production of lightweight but strong components, such as fairings and internal structural parts of aircraft.
Oil and gas industry: Due to its excellent chemical resistance, it is often used to make flexible piping and equipment components resistant to oil, gas and other corrosive fluids.
Automotive: In the automotive sector, nylon PA12 finds application in the production of interior and exterior parts of vehicles, such as engine components, linings and gaskets.
Sports and leisure: Due to its combination of strength and flexibility, it is used in the production of sports equipment, such as tennis rackets, gym equipment and bicycle parts.
Electronics: It is used as an insulating and protective material for cables, connectors and housings of electronic devices, due to its resistance to temperature and chemicals.
Fashion: Finally, it is widely used in the fashion industry, used for the production of strong and lightweight accessories such as belt buckles, glasses and shoe components.
Comparison with other materials
Resin: Resin is prized for its ability to create very precise details and for its smooth finish. However, nylon PA12 has superior strength and offers greater flexibility, making it more suitable for parts that must withstand high loads or wear.
ABS: ABS is a popular 3D printing material due to its strength and durability. However, nylon PA12 outperforms ABS in terms of abrasion resistance and chemical resistance. Furthermore, while ABS can be subject to warping during printing, nylon PA12 tends to offer better dimensional stability.
Why Choose Nylon PA12 for Your 3D Printing Projects?
Nylon PA12 is the ideal choice for those seeking a material that guarantees:
Durability: Resistant to wear and chemical agents, it is perfect for components that need to withstand repeated stress.
Dimensional Precision: With its low moisture absorption, it maintains dimensional stability even in challenging environmental conditions.
Flexibility in Applications: PA12 is suitable for both rapid prototyping and large-scale production of functional and industrial parts.
In conclusion, Nylon PA12 stands out for its combination of strength, durability, abrasion and chemical resistance, as well as its dimensional stability. Its mechanical properties make it an excellent choice for a wide range of 3D printing applications, from industrial uses to custom creations.
Choosing Nylon PA12 means opting for a material that combines strength, precision, and versatility. With Weerg, you can achieve high-quality 3D prints in PA12, thanks to advanced technologies and the expertise of our technicians, ensuring optimal results for every project.
VAPOR SMOOTHING FOR NYLON PA12
Chemical vapour smoothing, also known as vapor smoothing, is an essential finishing technique for enhancing the surface quality of nylon PA12 components produced through 3D printing. This method utilises heat and the condensation of vapour to smooth the surface of the printed part, reducing imperfections such as the porosity typical of objects created using the Multi Jet Fusion technique. During the vapour smoothing process, the component is placed inside an airtight chamber, where the vapour from a heated solvent is introduced. Upon contact with the surface of the part, the vapour condenses, slightly softening the surface due to the action of surface tension. This phenomenon helps to eliminate surface roughness and imparts a uniform and smooth finish. The duration of this treatment depends on the material used, the size of the component, and the desired level of finish. The result is a significant improvement in the aesthetic and sometimes functional properties of the finished nylon PA12 piece.
"Weerg Nylon PA12 3D printing service is outstanding! The speed and precision of the prints are amazing and the quality of the prints is superb. Highly recommend!"
NYLON PA12 PROPERTIES
Tensile breaking load | 50 MPa |
Modulus of elasticity | 2000 MPa |
Elongation at break | 15% |
Flexural modulus | 1730 MPa |
HDT 0.45 MPa | 175°C |
Izod impact resistance | 3.5 kJ/m² |
"Weerg Nylon PA12 3D printing service is remarkable! Results are incredibly fast and precise, and the quality of the prints is incredible. Five stars in my opinion!"
Questions and answers on NYLON PA12
Nylon PA12 is renowned for its exceptional mechanical properties, making it an ideal material for industrial applications and advanced prototyping. Among its primary strengths are its high-temperature resistance, which allows parts to perform reliably in thermally demanding environments, and its excellent dimensional stability, ensuring the production of components with highly precise and repeatable tolerances. This combination of attributes enables the creation of highly accurate and dependable 3D-printed parts.
In terms of mechanical strength, Nylon PA12 exhibits a tensile strength of 48 MPa, indicating its ability to withstand significant forces without deforming or breaking. This property makes it particularly suitable for structural applications. Additionally, its surface finish is of high quality, lending itself well to both functional and aesthetic end-use applications. The material also demonstrates good elasticity, with an elongation at break of 20%, which provides it with the ability to absorb deformation under load without compromising its integrity.
Its elastic modulus of 1700 MPa highlights the material's rigidity, while its flexural strength of 70 MPa and resilience of 45 kJ/m² make it a robust choice for applications requiring impact resistance and performance under dynamic stresses. Furthermore, with a Shore D hardness of 80 and a heat deflection temperature (HDT) of 175 °C at 0.45 MPa, Nylon PA12 offers a balance of durability and heat resistance, making it an excellent choice for components used in challenging environments or high-temperature conditions. This blend of qualities positions Nylon PA12 as one of the most reliable solutions for high-performance, precision-driven projects.
Nylon PA12 offers a broad range of finishing and colouring possibilities, making it highly versatile from both an aesthetic and functional standpoint. To enhance the surface quality of components, chemical vapour smoothing is a popular technique. This process, often referred to as "vapor smoothing," produces smooth and uniform surfaces by eliminating the rough texture typical of 3D printing. Not only does this treatment improve the visual appeal of parts, but it also reduces surface friction, a critical advantage for dynamic or moving components.
In terms of colouring, Nylon PA12 is available in its natural form as well as in white, providing extensive flexibility for customisation. The white version is particularly suitable for dyeing, allowing the creation of components in a wide array of shades. The dyeing process with specific pigments results in vibrant and uniform colours, which can be tailored to meet aesthetic preferences or branding requirements. Thanks to these options, Nylon PA12 can be customised to fulfil both visual and functional needs, making it an ideal choice for applications that require a balance of technical performance and attractive design.
Nylon PA12 is a thermoplastic material widely used in various applications due to its combination of mechanical strength, chemical stability, and versatility. One of its key areas of use is in industrial production through 3D printing technologies, particularly for functional prototypes and high-performance final parts. It is highly valued for its excellent chemical resistance to oils, greases, and hydrocarbons, which makes it particularly suitable for components operating in environments exposed to these substances.
Additionally, its high dimensional precision and mechanical strength make it ideal for applications requiring tight tolerances and durability, such as in industrial equipment and complex mechanical systems. Nylon PA12 is also a preferred choice for creating lightweight yet robust parts, especially in the engineering and electronics sectors, where its lightness and flexibility contribute to reducing the overall weight of products while maintaining high performance.
QUOTE IN 1 SECOND WITHOUT COMMITMENT
DON'T WAIT: UPLOAD YOUR 3D FILE AND GET A QUOTE FOR YOUR PARTS NOW!
Upload your 3D file to get one step closer to manufacturing your parts.
free instant quote