ULTEM
ULTEM 3D Printing: a versatile polymer for high-performance industries.
ULTEM™ PEI 9085 combines excellent thermal, mechanical, and chemical properties, making it ideal for complex applications in the automotive, aerospace, and transportation sectors. Its versatility makes it the ideal choice for innovative solutions across a wide range of industrial sectors.
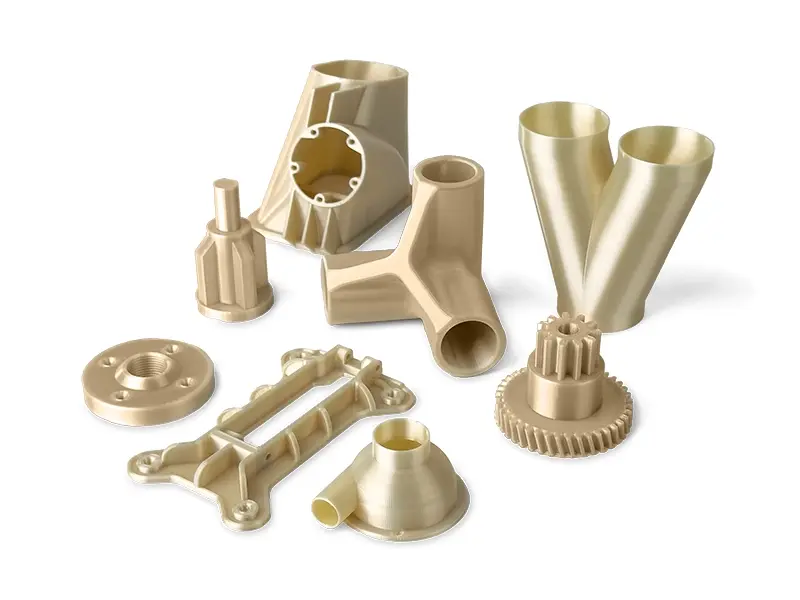
PROS
- Resistance to high temperatures
- Resistance to chemicals
- Certified to UL94-V0 (flame retardant), EN45545 (railway), FAR25.853 and OSU55/55 (aerospace)
- Good strength-to-weight ratio
- Excellent FST properties
CONS
- Expensive
- Break-away supports only
- Limited colours
MAIN FEATURES
- 3D printing process: FDM
- Layer height: 0,2 mm
- Tolerances: ±0,60mm < 100mm ; ±0,75% > 100mm
- Max size: 600 x 400 x 400 mm; 23,6 x 15,8 x 15,8 in
- Lead time: <3 days
- Infill: 100%
3D-printed Ultem video
High Thermal Resistance
One of the main advantages of ULTEM™ 9085 is its extraordinary ability to withstand high temperatures. The material can operate continuously up to 170 °C without losing its mechanical or structural properties, thanks to its high glass transition temperature and heat deflection temperature (HDT) that ensure its integrity even under extreme conditions. This feature makes it ideal for applications in the aerospace and automotive sectors, where components are subjected to intense thermal cycles and significant temperature fluctuations, ensuring reliable and long-lasting performance even in harsh environments.
Chemical Resistance and Dimensional Stability
It is distinguished by its excellent resistance to chemical agents, such as organic solvents, oils, acids and bases. This chemical robustness enables the material to maintain its properties even in aggressive environments, ensuring the durability and reliability of the components produced. Furthermore, its low coefficient of thermal expansion guarantees remarkable dimensional stability, making ULTEM well-suited for applications which demand consistent precision even in the presence of thermal variations.
Flame Retardant Properties (UL94-V0)
Another significant advantage of Ultem is its inherent flame-retardant property, certified according to the UL94-V0 standard. This feature ensures enhanced fire safety, making the material particularly suitable for applications where fire resistance is a fundamental requirement, such as in the transport and aerospace sectors as well as in regulated environments. The ability to halt the spread of flames not only contributes to operational safety but also improves the overall profile of the finished product, reducing risks in critical conditions.
Ultem material images
QUOTE NOW YOUR ULTEM PARTS
free instant quoteCOMMENT
ULTEM™ 9085 is a registered trademark of SABIC, which identifies a specific blend of polyetherimides (PEI), a high-performance thermoplastic polymer renowned for its unique combination of heat resistance, dimensional stability and chemical resistance. The material is highly valued not only for its mechanical and thermal properties, but also for its excellent characteristics during the 3D printing process. This product range is specifically formulated for applications that require high levels of reliability and performance, such as in the automotive, aerospace, mass transport (e.g. rail) sectors, and in applications that require resistance to high-energy radiation. ULTEM™ 9085 stands out due to its ability to maintain shape and functional properties even under extreme conditions, making it ideal for high-temperature operating environments.
Pros:
High Thermal Resistance: The ability to operate at temperatures up to 170 °C makes it ideal for extreme operating conditions. This feature is particularly valued in aerospace and automotive applications, where thermal fluctuations are common and can reach high levels. Its elevated glass transition temperature and HDT ensure that the material does not deform under thermal loads.
Chemical Resistance: The material is highly resistant to organic solvents, oils, acids, and bases, making it particularly well-suited for industrial applications where components may be exposed to aggressive chemical environments. This characteristic allows for a broad range of applications in chemically active environments, such as process industries and automotive applications.
Flame-Retardant Properties: The UL94-V0 classification confirms that Ultem possesses excellent fire resistance properties. This is a crucial element in many applications where fire safety is paramount, for example in public transport, the aerospace industry and other sectors governed by strict regulations.
Good Strength-to-Weight Ratio: Despite its robustness, it is characterised by a low specific weight (density of approximately 1.28 g/cm³), which makes it particularly competitive when minimising weight without sacrificing structural strength.
Quality and Precision in 3D Printing: In the context of 3D printing, especially for filaments designed for high-performance applications, it stands out for its extremely precise dimensions, consistent roundness, and excellent interlayer adhesion during printing. These aspects improve the final product’s quality and enable the production of components with complex geometries and tight tolerances.
Cons:
High Cost: One of the main drawbacks is the cost. ULTEM™ 9085, due to its advanced properties and the quality of the raw materials used, is significantly more expensive than many other thermoplastic polymers. This factor may limit its use in low-budget applications or mass production where cost is a crucial factor.
Limited Colour Availability: Currently, the colouring options for the material are rather limited, reducing the possibility for aesthetic customisation. For applications where visual appearance or brand graphics are important, this limitation might be a disadvantage.
Limited Break-Away Supports: The use of break-away supports in the 3D printing process with Ultem can be problematic, as support removal is less straightforward compared to other materials. This could affect the surface finish and require additional post-processing operations.
Applications and Sectors of Use
The wide range of properties of ULTEM™ 9085 makes it an excellent candidate for various applications, spanning from industrial areas to high-tech sectors. Among the main applications are:
Automotive Sector: Its use in automotive components, such as panels, engine parts and vehicle interiors, is favoured due to its heat and corrosion resistance. Its dimensional stability and the ability to perform in high-temperature environments make it an ideal material for critical components in modern vehicles.
Aerospace: In aerospace sectors, where low weight and mechanical strength are essential requirements, Ultem is used in structural components, cabin interiors and other elements that must operate under extreme conditions. Approvals such as FAR25.853 and OSU55/55 further guarantee its suitability in this sector.
Transport and Railway: Its applicability in the mass transport sector is also confirmed by the EN45545 approvals for use in railway applications. In this field, the material is used to produce components that require high fire safety and must maintain their mechanical and thermal properties over extended periods.
Comparison with Other High-Performance Materials: The Case of PEEK
An interesting and frequent comparison in the high-performance polymer field is between ULTEM™ 9085 and PEEK (polyetheretherketone). Both materials offer excellent thermal and mechanical properties, but there are substantial differences:
Thermal and Operational Resistance: While ULTEM™ 9085 can withstand continuous temperatures up to 170 °C, PEEK can typically operate at even higher temperatures, reaching up to 250–300 °C in certain cases. This difference makes PEEK more suitable for applications requiring extreme temperature resistance, although it also implies higher energy and processing costs.
Cost: In addition to its outstanding technical performance, PEEK is significantly more expensive than ULTEM™ 9085. The high cost of PEEK limits its use to niche sectors where thermal and mechanical performance are indispensable requirements, whereas Ultem occupies a slightly more accessible price range while still offering excellent performance.
Processability: Ultem is renowned for its better processability, especially in the context of 3D printing. Its characteristics in forming high-precision filaments, the good adhesion between layers and the optimal flow behaviour during extrusion make it ideal for complex and rapid manufacturing. By contrast, PEEK requires more stringent processing conditions (very high nozzle and platform temperatures) and is less suited to rapid prototyping.
Sectoral Applications: Although both materials find use in advanced sectors such as aerospace and medical, PEEK is often chosen for applications where sterilisability, biocompatibility and chemical resistance in extremely aggressive environments are primary requirements. ULTEM™ 9085, while offering notable mechanical and thermal properties, is preferred in fields where a balance between cost and performance is essential, maintaining strong competitiveness in the automotive, transport and 3D printing sectors.
Radiation Resistance: A further technical aspect is resistance to high-energy radiation. Both materials deliver good performance in this field, but the specific formulation of Ultem ensures additional resistance under conditions where radiation degradation could otherwise compromise the component’s functionality. This makes Ultem particularly suitable for applications in sectors with high radiation exposure, such as certain aerospace environments.
Conclusion
ULTEM™ 9085 represents an excellent solution in the field of high-performance thermoplastic materials. Its superior mechanical and thermal properties make it an ideal candidate for numerous industrial applications, from the manufacture of automotive and aerospace components to advanced 3D printing technologies. The material stands out for its dimensional stability, high resistance to chemical agents, and considerable ability to operate under extreme conditions, qualities that position it as a benchmark in the technical polymer sector.
The comparison with other high-performance materials, such as PEEK, highlights how ULTEM™ 9085 offers an attractive balance between technical performance and cost. Although PEEK excels in terms of thermal resistance and compatibility with extreme environments, its high cost and processing complexity make it less suitable for applications where budget is a critical factor. In this context, Ultem presents itself as a viable alternative, particularly in applications where processability, compatibility with 3D printing, and a strong balance between cost and performance are decisive.
Among its main advantages is also its inherent flame retardant property, which ensures enhanced operational safety in regulated sectors where fire prevention is a priority. However, issues such as the high cost and limitations regarding aesthetic customisation (colour, break-away supports) remain critical points that may influence the final decision of the designer or engineer when selecting the material.
In conclusion, ULTEM™ 9085 is an extremely versatile and high-performing material, capable of meeting the demands of sectors where the combination of strength, thermal stability and processability is indispensable. Its growing adoption, particularly in 3D printing for industrial applications, testifies to the market’s confidence in its properties and its ability to operate under extreme conditions without compromising performance.
ULTEM PROPERTIES
Density | 1,28 g/cm³ |
Modulus of elasticity | 2439 MPa |
Elongation at break | 70% |
Flexural strenght | 129 MPa |
HDT 0,45 MPa | 169°C |
Charpy impact strength | 10 kJ/m² |
Questions and answers
Ultem is SABIC’s registered trademark for a family of high-performance thermoplastic materials, made primarily from polyetherimides (PEI). These polymers are designed to ensure high thermal resistance, dimensional stability and chemical resistance, making them ideal for applications in extreme and high-performance environments, such as the aerospace, automotive and transport sectors.
Ultem stands out for its high-level mechanical and thermal properties:
-
Mechanical Resistance:
The material exhibits high elongation at break (around 70%), a modulus of elasticity of approximately 2439 MPa and bending strength of 129 MPa. These figures indicate that Ultem has a good capacity to withstand mechanical stresses, retaining its shape and functionality even under stress. -
Thermal Resistance:
Ultem is able to operate continuously at temperatures up to 170 °C, and it maintains dimensional stability thanks to its low coefficient of thermal expansion.
In summary, Ultem is extremely resistant both mechanically and thermally, making it suitable for severe operating environments.
Ultem’s wide range of applications spans numerous sectors, thanks to its combination of strength, dimensional stability and chemical resistance. In particular:
-
Automotive Sector:
Used for components that require high thermal and mechanical resistance, such as panels, interior parts and structural components. -
Aerospace Sector:
Employed in critical applications where low weight, dimensional stability and high resistance to elevated temperatures are essential. -
Mass Transport and Railway:
Utilised in applications that demand high safety standards, including fire resistance and stability under thermal and mechanical stresses.
Yes, Ultem 9085 possesses intrinsic flame retardant properties and achieves the UL94-V0 rating, certifying its fire resistance. This makes it particularly well-suited for applications where fire prevention is a fundamental requirement, such as in the transport, aerospace and other high-safety industrial sectors.
QUOTE IN 1 SECOND WITHOUT COMMITMENT
DON'T WAIT: UPLOAD YOUR 3D FILE AND GET A QUOTE FOR YOUR PARTS NOW!
Upload your 3D file to get one step closer to manufacturing your parts.