TPU
Thermoplastic polyurethane: flexibility and strength
TPU (thermoplastic polyurethane) combines softness, elasticity, and durability. It is the ideal solution for components that must withstand mechanical stress while maintaining flexibility and comfort, such as sleeves, shock absorbers, and moving parts.
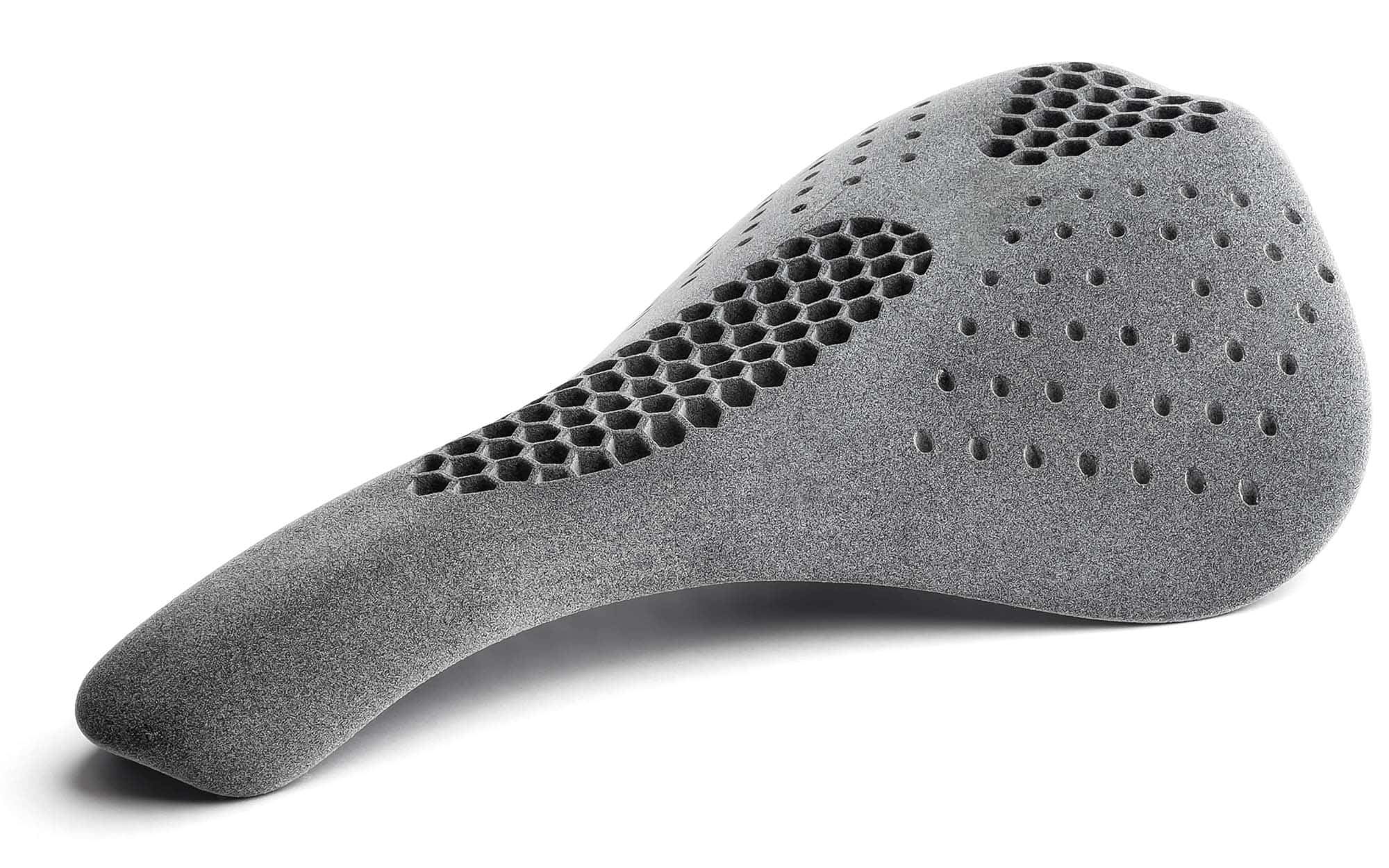
PROS
- Geometric freedom typical of HP MJF
- Shore 88/90A flexible material
- Suitable for absorbing shocks and damping vibrations
- Excellent resistance to UV and hydrolysis
CONS
- Limited flexible behaviour for thick sections
- High warping risk on large, wide and thin parts
MAIN FEATURES
- 3D printing process: MJF
- Tolerance: ±1,00mm < 100mm ; ±1,00% > 100mm
- Max size: 380x284x380mm; 15x11.2x15in
- Lead time: <5 days
- Available finishes: Vapor smoothing
TPU 3D PRINTED VIDEO GALLERY
Extreme design freedom
Explore complex and unexpected shapes without the need for supports, making surprising custom parts and prototypes quickly and accurately. Express your creative potential and shape your ideas with MJF technology on TPU.
Time to market reduced by 90%
Designers know how difficult and expensive testing a soft, flexible material can be: 3D printed TPU not only solves the problem for prototyping, but in many cases can be cost-effective in production runs.
Suitable for absorbing shocks and damping vibrations
It is perfect for designs that require flexibility and adaptability. Thanks to its high elasticity and flexibility, it is great for absorbing shocks, damping vibrations, and resisting weathering, UV rays, and some chemicals. It's highly resistant to tearing, making it ideal for pieces that need to be flexible and adaptable as for the piece in the video.
QUOTE NOW YOUR TPU PARTS
free instant quoteTPU IMAGE GALLERY
COMMENT
TPU, an acronym for Thermoplastic Polyurethane, is a plastic material distinguished by its exceptional properties of flexibility, strength and durability. This material offers a series of unique advantages that make it ideal for applications ranging from footwear production to the medical industry and much more.
Advantages of TPU in 3D printing
Geometric Freedom Typical of HP MJF 3D Printing: 3D printing with HP MJF technology allows you to fully exploit the properties of the TPU material. This technology offers extraordinary geometric freedom, allowing the creation of complex parts without the need for additional supports. This capability is crucial for engineers and designers who can create intricate components efficiently.
TPU flexibility: The TPU material is known for its exceptional flexibility, with a Shore hardness of 88/90A. This characteristic makes it ideal for applications that require a material that is both flexible and durable. Its ability to adapt to different shapes and designs makes it perfect for a wide range of uses, from mechanical components to protective devices. The 3D printing of TPU offers maximum adaptability, ensuring that your creations can meet the specific requirements of your project.
Suitable for Impact Absorption and Vibration Damping: Thanks to its remarkable elasticity, TPU can absorb impacts and dampen vibrations. This feature makes it an excellent choice for parts and components that must withstand mechanical or dynamic stress. In applications where safety and durability are paramount, TPU provides reliable protection against impact damage or unwanted vibrations. Its ability to absorb impacts makes it an ideal material for applications where safety and structural integrity are a priority.
Excellent UV and Hydrolysis Resistance: TPU offers exceptional resistance to damage from UV rays and hydrolysis. This means that the material maintains its integrity and durability even in outdoor environments or when exposed to direct sunlight. UV resistance is particularly crucial for outdoor applications, such as automotive components or parts exposed to the external environment. Additionally, hydrolysis resistance makes 3D printed TPU suitable for applications that require high resistance to water and humidity. This combination of properties makes it a versatile and reliable material for a wide range of uses.
Cons
Behavior Limited on Thick Sections: It is important to note that in particularly thick sections, the flexible behavior of TPU may be slightly limited. In such situations, careful consideration of this aspect during part design is crucial. Engineers and designers should evaluate the need to reinforce thicker sections or explore alternative solutions to ensure that TPU meets the specific requirements of the application. Understanding the material's limitations is essential for achieving optimal results.
Available Only in Rough Gray Color: Currently, TPU printing is primarily available in a rough gray color. This limitation may impact aesthetic options for some projects, especially when a broader range of colors is required for design purposes. However, many applications prioritize functionality over aesthetic appearance, and gray TPU polymer can still offer exceptional performance for many of them. In cases where color choice is critical, post-processing options or exploring other material alternatives may be necessary.
Risk of Deformation on Extended, Wide, and Thin Parts: In the presence of very extended, wide, or thin parts, there is a potential risk of TPU deformation during use or production. It is advisable to consider this aspect during material utilisation and design. Engineers can implement design strategies to minimise the risk of deformation, such as using structural reinforcements or special geometries. Additionally, optimising printing parameters and paying attention to printing temperature can help reduce this risk. Planning and prevention are fundamental to ensuring that TPU meets the specific project requirements without deformation or distortion issues.
Applications
Flexible materials, including TPU, stand out for distinctive features that make them particularly suitable for a variety of applications. These materials are known for their high elongation at break, which means they can be significantly stretched before breaking. Additionally, they have a low elastic modulus, which means they regain their original shape after deformation. These properties make them ideal for applications that require a certain level of elasticity and resistance to deformation.
The advanced properties of flexible materials make them a valuable choice in many industries. The combination of flexibility and strength is essential in applications ranging from the automotive industry, where components must withstand vibrations and impacts, to the production of medical devices, where compliance and safety are paramount. The ability to adapt to complex shapes and absorb impacts makes flexible materials a valuable resource for engineers and designers seeking innovative solutions to their design challenges.
Comparison with other materials
Footwear: In the footwear industry, TPU is widely used for the production of soles and inner inserts. Its softness and ability to adapt to the shape of the foot make it ideal for ensuring comfort and durability in both sports and everyday footwear.
Medical Devices: It finds applications in the creation of gaskets, prosthetics, and orthopedic devices. Its adhesion between layers and resistance to abrasion are crucial in medical applications where durability and safety are essential.
Sportswear: In the sportswear sector, TPU polymer is used for the production of elastic bands, straps, and other accessories. Its flexibility allows for the creation of comfortable and durable products that support physical activity.
Industrial Sector: TPU's industrial applications are diverse, including protective coatings for machinery and parts that require significant wear resistance. TPU can withstand adverse environmental conditions and extend the lifespan of industrial components.
Automotive Sector: In the automotive industry, TPU polymer is used in the production of gaskets, grommets, and interior and exterior coatings. Its abrasion resistance and flexibility make it ideal for components subjected to mechanical stress.
Electronics: TPU can be used in the production of protective shells for portable electronic devices, providing a combination of flexibility and impact protection.
Conclusion
In conclusion, TPU, or Thermoplastic Polyurethane, stands out as an excellent choice for a wide range of projects that require a combination of softness, flexibility, and durability. This material offers a series of unique advantages that make it ideal for applications ranging from footwear production to the medical industry, and much more.
Among its benefits, TPU provides extraordinary geometric freedom typical of 3D printing with HP MJF technology, allowing for the creation of complex components without the need for additional supports during printing. Its exceptional flexibility, with a Shore hardness of 88/90A, makes it perfect for applications requiring adaptability and resilience. Additionally, it can absorb impacts and dampen vibrations, offering reliable protection against damage from impacts or dynamic stresses. Its remarkable resistance to UV rays and hydrolysis ensures the material's durability even in outdoor environments or direct sunlight exposure.
However, it is crucial to consider some limitations, such as limited flexibility in thick sections, predominantly available in a rough gray color, and the risk of deformation in extensive, wide, or thin parts. Engineers and designers must be aware of these challenges and plan accordingly.
Ultimately, flexible materials like TPU offer a valuable alternative in many industrial applications. Their combination of flexibility and strength is essential in industries ranging from automotive to sports apparel and medical devices. Despite the specific challenges of 3D printing with flexible materials, their ability to adapt to complex shapes and absorb impacts makes them a valuable resource for engineers and designers seeking innovative solutions to their design challenges. Compared to other materials, TPU stands out for its versatility and its ability to meet a wide range of application needs in various industrial sectors.
"I would highly recommend Weerg to anyone looking to make high quality TPU parts."
TPU PROPERTIES
Tensile breaking load | 9 MPa |
Modulus of elasticity | 85 MPa |
Elongation at break | 280% |
Flexural modulus | 75 MPa |
HDT 0.45 MPa | Not applicable |
Izod impact resistance | No break |
"Thanks to Weerg, I can make parts with TPU that are both flexible and durable - perfect for my needs!"
Questions and answers
TPU (Thermoplastic Polyurethane) is a thermoplastic elastomer that combines flexibility, durability, and technical performance. It is a flexible material with a Shore hardness of 88/90A, making it ideal for applications requiring elasticity and controlled deformation capability. TPU is particularly suitable for absorbing shocks and damping vibrations, providing reliable performance in dynamic applications or those with repetitive motion. Additionally, it has excellent resistance to UV rays and hydrolysis, making it an optimal choice for prolonged use in outdoor environments or in the presence of moisture. Thanks to these characteristics, TPU is widely used in sectors such as automotive, robotics, and the production of technical consumer goods.
TPU (Thermoplastic Polyurethane) differs from other elastic materials like TPE (Thermoplastic Elastomer) and traditional rubber due to its unique properties. Compared to TPE, TPU is generally more durable and resistant. It has greater abrasion resistance and UV stability, making it ideal for outdoor or high-wear applications. Additionally, TPU offers a broader range of Shore hardness levels, allowing for more precise customisation of its elastic and mechanical properties. Unlike TPE, TPU is more dimensionally stable and less prone to deformation under prolonged load. Compared to traditional rubber, TPU is more versatile as it can be processed through thermoplastic methods, while rubber typically requires vulcanisation processes. TPU also provides better chemical and hydrolysis resistance as well as greater elongation, making it more suitable for advanced technical applications. However, traditional rubber may have an advantage in extreme temperature environments or for specific applications requiring higher rigidity.
TPU is an extremely versatile material and is used in a wide range of applications requiring elasticity, strength, and durability. It is particularly suitable for producing flexible and durable components, such as seals, shock absorbers, and o-rings, that must absorb shocks and damp vibrations. In the industrial sector, TPU is often employed to create flexible hoses, and protective coatings due to its ability to withstand wear, repeated bending, and hydrolysis. In the automotive industry, it is used for components like bellows, cable sleeves, and protective covers, where flexibility combined with chemical and thermal resistance is required. TPU is also a popular choice for sports equipment and footwear, where its elasticity and shock-absorbing capabilities enhance performance and comfort. Other applications include functional prototypes, electronic devices with flexible protective coatings, and technical items such as elastic belts and connectors.
QUOTE IN 1 SECOND WITHOUT COMMITMENT
DO NOT WAIT: UPLOAD YOUR 3D FILE AND GET A QUOTE FOR YOUR TPU PARTS NOW!
Upload your 3D file to get one step closer to manufacturing your parts.
free instant quote